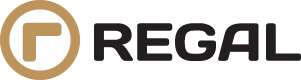
With a nationwide support network, better environmental emissions and ultimate driver safety and comfort, the Volvo FM500 was the obvious choice for Regal.
At Regal, our drivers cover 11 million kilometres per annum. At an average of 60km/hour that’s a lot of hours in the cab. To ensure our team’s safety and maximise our productivity, our drivers need to be in the best vehicle there is.
Each year, Regal’s transport team would source vehicle specifications from multiple dealerships in a bid to meet our requirements for the coming year. The team would consider multiple factors including fuel efficiency, load capacity, repair and maintenance requirements and lifetime cost, in an effort to highlight the best option. If these specifications were comparable, the choice was narrowed down according to price, tare weight and after sales support.
This was a time consuming process and over the years had resulted in a fleet with 10 different makes of vehicle.
Each Regal vehicle had been carefully chosen to meet all specifications required, but a multi-brand fleet, which had been purchased on an ad hoc basis as financials allowed, brought issues of its own. Multiple support networks were required to service the different makes and models, as was a large parts inventory and an extremely broad product knowledge required within our mechanical team. We knew that unless a significant capital expenditure programme was adopted, the average age and repair and maintenance required for the fleet were statistically likely to worsen.
“An aging fleet was resulting in increasing R&M costs, particularly as the vehicles needed to meet changing environmental emissions regulations,” explains Rian Alexander, Asset Manager for the Regal Group. “With lots of changes happening around engine technology, we had multiple options that were all very new to New Zealand but which hadn’t been tested in our environment. We were conscious that a poor decision here could result in 10 years (rough truck life) of issues to deal with.”
"We've been very impressed with the Volvo FM500. They meet our values of being safe and responsible - and they look good too!
"
Embarking on a new fleet required input from all areas of the business. The key variables which had previously been evaluated for any truck purchase needed to be reconsidered and different departments had different requirements.
“It was agreed that our previous key points (price, tare weight and after sales support) were still important but we needed to add to these,” says Rian. “The new list included driver acceptance, safety, whole cost of life (not just purchase cost), a national support network, reliability (in other words more time on the road), and a preference for one make/model to be able to service all requirements, thus dramatically reducing parts stock requirement over time.
“From this, we built a generic specification sheet and identified three potential suppliers. We then asked them to provide proposals to supply an initial two-year contract.”
Two proposals were very compelling. One was cheaper but upon further analysis, the team discovered that the more expensive truck, when considered over its entire life, was much better value.
The winning make/model was the Volvo FM500.
“This truck gave us extreme driver comfort and acceptance,” says Rian. “This was important because an earlier issue had been driver retention. Drivers were leaving the company to drive a better truck elsewhere. Additionally, with Volvo scoring exceedingly well on the safety front we could be confident we had done our bit in ensuring a safe work environment for our drivers and that should they be involved in an accident they stood the best chance possible of survival.”
The chosen brand also meant Regal had one platform that could accommodate any configuration required, a nationwide support network that included contact, warranty and invoicing, and a lengthened service interval from 20,000km to 40,000km.
What’s more, Regal has reduced its mono-nitrogen oxides (NOx) by 80% across the Volvo fleet and achieved a 60% reduction in particulate matter when compared to older fleet.
“Since the first purchase in 2012, we now have over half of the fleet converted to Volvo,” says Brett McHardie, joint owner and managing director of Regal. “To date, we have not had one driver complaint regarding the product. In fact, we have had drivers who, historically, would only drive a particular brand of truck reluctantly trial a Volvo only to return and say ‘I don’t want my old truck back.’”
Volvo’s Dynafleet application has also been an added bonus for Regal. This online Transport Information System accurately measures the performance of each driver, scoring them out of 100 for their driving ability, whatever road or terrain they are on. This includes elements such as fuel consumption, braking time, and speed average. Just as valuable is Dynafleet’s vehicle tracking tool.
“The Dynafleet app allows us to see the exact location of each of our trucks from any mobile device. Although we have a dedicated GPS tracking system, this mobility is a major advantage for our logistics team,” says Brett. “It has improved our management of the vehicles as it takes the variables out. We currently have the technology in 30 of our trucks and plan to have it installed in every new truck.
“We’ve been very impressed with the Volvo FM500. They meet our values of being safe and responsible – and they look good too!”>
Volvo’s in cab remote has allowed our manufacture team to set up all major body builder functions to be run from a remote. These include hoist operation, tail door opening, cover operation etc.
Now the driver has options. Although these operations can still be performed from the comfort of the driver’s seat, when applicable the driver can perform these operations outside the cab whilst keeping a closer eye on the job. Examples of where this technology has been particularly beneficial include; when unloading in low sheds where roof clearance needs to be closely watched, tipping over a grate where overfilling is an issue, and grain hatch deliveries.
In all situations the driver can keep a close eye on what’s happening, where it’s happening and still be in full control of what is going on.