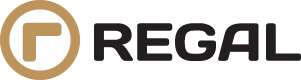
Regal weighs in on latest innovation with design of smartphone operated in-cab weigh system.
Managing the weight of a truck’s load is an integral part of every driver’s role here at Regal. The weight of a truck has a real impact on its fuel consumption and haulage ability.
It is also an industry regulation we must abide by. The New Zealand Transport Agency (NZTA) has strict regulations on the weight of a load for safety, infrastructure and environmental reasons. This means an overloaded truck can result in significant fines, while an underloaded truck can result in loss of revenue.
When our drivers are loading trucks, they do so on a weigh bridge, enabling them to monitor the weight of each load. However, there are some situations where there isn’t a weigh bridge for our drivers to use, for example when loading in a paddock.
To remove the guesswork from our drivers, and the risk of fines or revenue loss, Regal’s design team were tasked with a challenge. To come up with a system that would allow the drivers to achieve an accurate weight of their loads.
The result was an in-cab weigh system, designed in conjunction with Tait Controls.
This was nothing new – other systems are available on the market – but Regal’s was better.
Rian Alexander, Regal’s workshop manager, says other systems available use expensive load cells that require significant modification to fit.
“Although the technology is there, whenever a load cell needs to be implemented, not only is it an expensive system but it requires the vehicles to be off the road for some time while the system is being set up.
“We wanted to create a system that was easier to use, required minimal setup but still provided our drivers with the precise weight and measurements they needed to load safely.”
"We’re excited to see where this technology can take us.
"
Regal’s in-cab weigh system provides details of all axle set weights, individual truck, trailer and unit weights, and truck and trailer payloads. It also tells drivers how heavy the truck is to prevent over or underloading.
“The in-cab weigh system takes pressure from individual axle set airbag suspensions and hydraulic ram pressure in the truck. A calibration calculation then converts these pressures to weights which are displayed to the driver on the screen of the in-cab smartphone,” explains Rian.
“Our system requires the fitting of two plastic boxes, one to the truck and one to the trailer. Connected to these boxes are power and pressure lines and the install is completed in a matter of hours.”
Once installed, the unit is calibrated at the weigh bridge of our bulk store at the Mount and is then ready to go.
A bonus feature of the system is the ability it gives drivers to monitor the weight of the hi unit from anywhere within range of the truck. “This allows them to self-load under a hopper without the need to return to the cab or speak to a loader driver as he is being loaded. It also gives drivers an accurate measure of weight, which is particularly important if there is no weigh bridge when loading.”
The system is currently operational in a small handful of units. Almost 30 other vehicles have the system installed but are waiting calibration. Further developments of the system are underway to make it available in our non-tipping units.
“Potential further development of the system could include automatic communication of weights back to base and sending of maximum allowable weights for certain jobs out to trucks running HPMV (Heavy) permits,” says Rian.
“We’re excited to see where this technology can take us.”