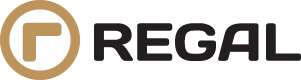
With the increasing demand for high-cube units, Regal’s design engineers took on the task of creating one of the lightest large volume units in the market.
Simple to manufacture and encompassing all the best ideas our engineers have tried and tested, this unit comes off the back of the design of our most versatile unit to date, the first of its kind in New Zealand.
Here at Regal, we have a proud history of innovation and nowhere is this more evident than in the two most recent additions to our fleet: #536 and #537.
We recently tasked our design and engineering teams to create two units, neither of which had been done before. The first, #536, needed to be a versatile unit which could cart both bulk and freight; the second, #537, needed to maximise the volume of loads while reducing the number of ‘corners’ within the bin.
True to form, our team were up to the task and built two very different and very unique units, both of which enable us to deliver unparalleled logistical solutions for our clients.
The brief: to design Regal’s most versatile unit possible. A non-tipping, multi-product cartage unit, that could accommodate a diversity of both bulk and freight, from woodchips to fertiliser, timber to grain.
The challenge: it had never been done in New Zealand before.
Enter Regal design engineer, Max Krotov. Two years out of university, Max was up for the challenge. Six months of research, design and reworking his drawings, Max knew this unit was going to be very different. “Everything was new,” he says. “Because it had never been done in New Zealand before, all I had to go off were pictures I could find of other units around the world, and parts needed to be sourced from overseas too.”
Regal’s engineering and mechanical teams overcame any unexpected challenges along the way and pushed the boundaries of innovation on a daily basis. “The nature of the moving floor and side door unit set high demands,” says Max. “Tolerances were low and so were margins for error, but despite these challenges Regal’s workshops delivered.”
"“The nature of the moving floor and side door unit set high demands. Tolerances were low and so were margins for error, but despite these challenges Regal’s workshops delivered.”
"
The brief: to develop a large volume unit that was lightweight and simple to manufacture. All while maximising volume of load and reducing the number of ‘corners’ inside the bin where product might stick.
The challenge: to achieve near-perfect weight distribution at maximum legal height and width, while enabling the unit to safely tip under the same roofs as smaller units do.
“This design has encompassed all the best features and ideas the Regal team have tried and tested on our previous units,” says Max. “It’s a combination of our old high-cube fleet, automats and the latest walking floor. Compared to the old high-cubes, the manufacturing process has been turned upside down.”
“Form wise, this unit creates a sense of consistency across our whole new high-cube fleet,” says Max. “It’s believed to be one of the lightest units in New Zealand, and furthermore it’s one of the best-looking units on the road too, on par with #536 of course.”
Regal’s engineering and mechanical teams have proved innovation is at their core and, to continue to solve high volume storage and transport needs for our clients, we can expect more first-of-a-kind units to emerge from Regal’s workshops in the near future.
What makes 536 unique?
What makes 537 unique?