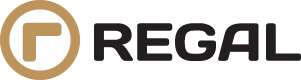
To be innovative is a core value of the work we do at Regal. Our design team’s talent came on display with the development of a high cube automat unit.
At Regal, much of the work we do is carting light weight products such as wood chip, rubbish and recycling. Demand for this service has increased over the last five years so larger cubic capacity became essential.
Our in-house design and manufacturing team was faced with the challenge of creating a maximum cubic capacity unit which could carry bulk commodities without needing to tip when unloading, improving the safety and efficiency of our services.
Regal’s existing high cube units were all tipping units, whereby the tipper body and payload would lift at the front by hydraulic ram. This allowed the product to slide out the back of the body.
However, as these units became larger over the years, longer and higher bodies resulted in increasingly higher maximum tip heights – the distance from the ground to the top of the body when fully tipped.
Wil Ashcroft, design engineer at Regal, says this caused a number of issues.
“When tipping in sheds, the units needed internal roof heights of up to 10metres, which is very rare. Existing units were struggling and damage caused to sheds and vehicles was becoming a regular issue.
“Unit stability was another concern. Although none of the existing units had fallen over, the longer and higher we went with the design the greater the risk, particularly when unloading on uneven/unstable ground or during strong winds.”
"Our design philosophy at Regal is very unique and it is units like this that really showcase what our in-house design and manufacturing team are capable of,
"
Regal’s in-house design and manufacturing team came up with a completely new design of a high capacity unit. It is based on tried and tested Automat technology, which is used in the fertiliser industry, but, to our knowledge, has not been used for such a large unit before.
“Once the prototype was complete we worked through various minor issues in order to ensure reliable and consistent operation,” says Wil. “This was completed over a period of three months while the unit was operated semi-locally.”
Various modifications and upgrades were undertaken to the unit following this trial period and these upgrades are being developed further for use in the next upgraded production of this model, scheduled to hit the road July 2016.
The final version of the high capacity automat design unit had a ‘live floor’.
“This ‘live floor’ allowed the product inside the unit to be ejected. This was done by pulling a large conveyor mat, which covered the entire floor of the unit, out of the back and rolling it up at the rear,” says Wil.
Other improved design elements included:
Lower unload height: The new unit was designed to be more accommodating of lower roof heights. Previously a roof height of 9.5m was required to unload the unit, but the newer unit only requires a roof height of 4.25m.
Greater cubic capacity: “We have increased cubic capacity and payload by 12% when compared to our previous largest unit. This was already 25% larger than the industry standard high cube unit. Essentially a job that would have historically required four loads to be carted can now be easily achieved in three” Wil says.
Improved weight distribution: There has been an improvement in axle weight distribution, which has resulted in near perfect axle loading at maximum allowable weights. Any stability concerns when unloading are also a thing of the past.
“Our design philosophy at Regal is very unique and it is units like this that really showcase what our in-house design and manufacturing team are capable of,” says Wil.
“Not only does it make for a safer work environment for our staff and our clients, it also improves the services we can deliver to our customers. We’re really pleased with the result.”